Explore the fundamentals of strain gauges, their types, working principle, configurations, components, and various applications in engineering and science.
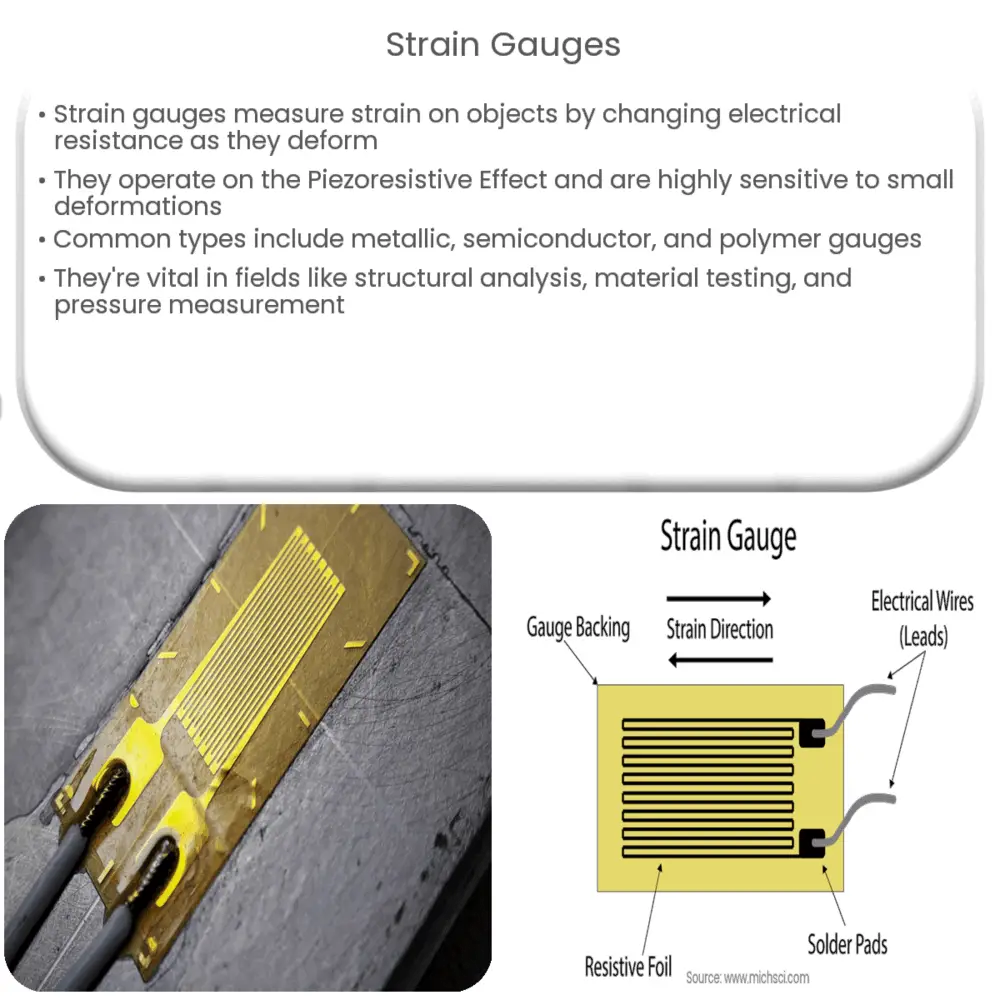
Introduction to Strain Gauges
A strain gauge is a versatile tool used in engineering, physics, and material science to measure strain on an object. The principle behind its operation is fairly straightforward – as an object deforms, the strain gauge deforms with it, thereby changing its electrical resistance. This change can be accurately measured and directly correlated to the strain experienced by the object.
The Working Principle of Strain Gauges
The working principle of a strain gauge revolves around the physical property of conductive materials: as a conductive material stretches or compresses, its electrical resistance changes. This is known as the Piezoresistive Effect. It’s essential to note that strain gauges are exceptionally sensitive to small deformation changes, making them ideal for monitoring and measuring in many industrial and scientific applications.
Types of Strain Gauges
Metallic Strain Gauges: These are the most common type of strain gauges, consisting of an insulating flexible backing which supports a metallic foil pattern. When the object under test is subjected to stress, the resulting strain directly deforms the foil, causing its electrical resistance to change.
Semiconductor Strain Gauges: Made up of semiconductor materials, these strain gauges exhibit a much higher gauge factor than metallic strain gauges, which makes them highly sensitive. However, their temperature sensitivity and non-linear output require additional compensations and careful handling.
Polymer Strain Gauges: These gauges use a conductive polymer material that changes its resistance when stretched. They offer a compromise between the benefits and drawbacks of metallic and semiconductor gauges.
The Components of a Strain Gauge
A typical strain gauge consists of the following key components:
The Gauge Factor (GF) which is a property of the gauge material, correlating the ratio of relative change in electrical resistance to the mechanical strain.
The Backing, which supports the resistive element. It must be flexible and capable of adhering to the test object.
The Resistive Element, which is the metallic foil that deforms with the strain and causes a change in electrical resistance.
The Adhesive, which secures the gauge to the test object. It should ensure good bonding and transmit the strain efficiently.
Strain Gauge Configurations
Strain gauges are typically installed in specific configurations to maximize their efficiency and effectiveness. These configurations are primarily designed to reduce measurement errors due to temperature changes or unwanted strain in non-measured directions. Here are the main types:
Quarter Bridge Configuration: This involves one active strain gauge and three passive resistors. It’s the simplest configuration and measures strain in one direction.
Half Bridge Configuration: This configuration uses two strain gauges. It compensates for temperature changes and can measure strain in two perpendicular directions.
Full Bridge Configuration: Four strain gauges are used, offering the highest sensitivity and compensating for temperature changes and unwanted strains. This configuration is typically used in high-precision measurements.
Applications of Strain Gauges
Due to their sensitivity and versatility, strain gauges have a wide range of applications. These include:
Structural analysis and stress testing of bridges, aircraft, and other mechanical structures.
Material testing in laboratories, measuring the tensile and compression properties of materials.
Load cell sensors in weighing scales and industrial measurement applications.
Pressure measurement in pressure vessels or gas cylinders.
Torque measurement in engine shafts.
Conclusion
In conclusion, strain gauges are a fundamental tool in various scientific and engineering fields. Their ability to accurately measure strain through the principle of piezoresistivity enables the prediction and monitoring of stress and structural integrity in various materials and structures. Although their application requires understanding of their types, components, configurations, and potential measurement errors, their high sensitivity and versatility make them an indispensable part of modern measurement technology.